Client: Bar Juice
Project Overview:
Bar Juice, a large distributor shipping numerous boxes to retail stores, experienced frequent errors in their shipments, with products being over- or under-delivered. Stearns Digital analyzed the company’s workflow and recommended the development of a custom picking system to ensure shipment accuracy and alignment with sales orders.
Implementation:
We implemented a barcode-driven picking system, where users would scan boxes using a wireless barcode scanner and tablet. The system displayed real-time feedback, showing the number of boxes scanned for each product and immediately highlighting any discrepancies for correction. This allowed operators to quickly add or remove boxes as needed, ensuring accurate shipments.
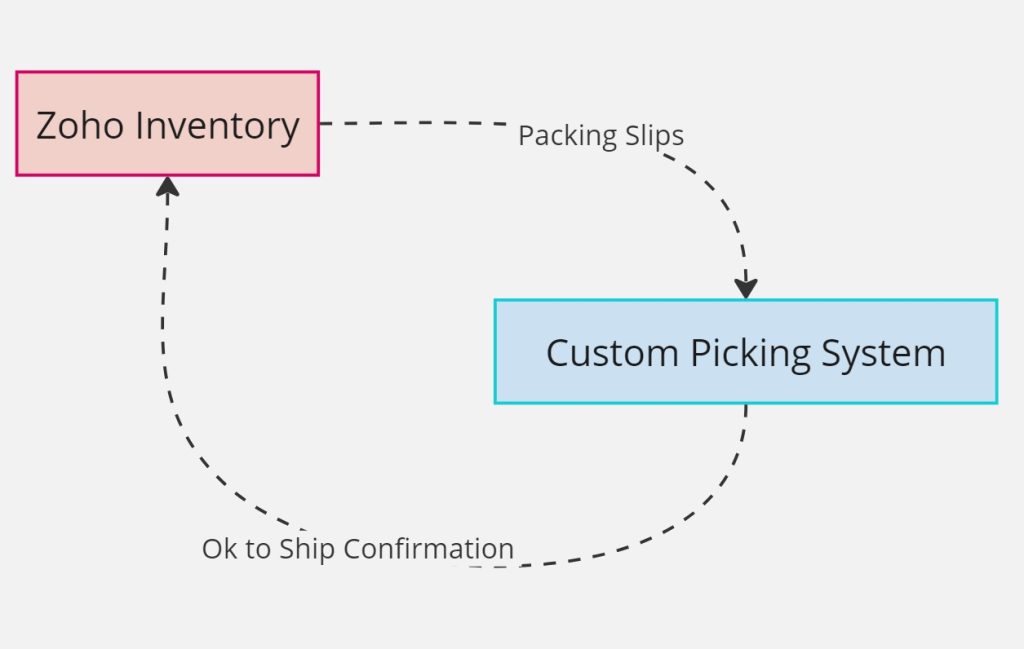
One of the main complexities was integrating the custom system with Zoho Inventory via API access to retrieve Packing Slips. After verifying the packing was correct, the user could mark the shipment as “Shipped” in our system, which automatically updated Zoho Inventory, thus eliminating the need to switch interfaces and streamlining the entire workflow.
Technologies Used:
- Zoho Inventory API
- Wireless Barcode Scanner
- Tablet-Based Web Application
- Real-Time Data Processing
Results:
The implementation of this web-based system reduced picking errors significantly, improved shipment accuracy, and enhanced workflow efficiency by reducing manual interventions and the need to switch between systems. By seamlessly integrating with Zoho Inventory, the solution provided greater speed and accuracy, contributing to a more reliable distribution process for Bar Juice.
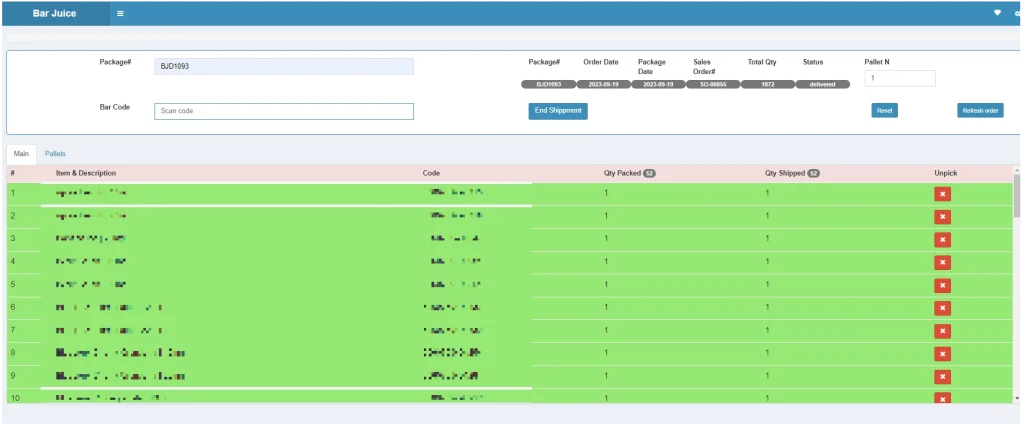
Leave a Reply